In the "fabulous" research project, M.TEC is working together with the participating project partners on the development of function-integrated drive components for electromobility. The aim is to reduce the weight of electric motors and wheel hub motors. Metal components are to be replaced by high-performance composite materials made from carbon fiber tapes. This will make the electric vehicle lighter, more efficient, more robust and more agile overall.
Electromobility: Drive and challenges
Mobility nowadays is being rethought: According to the German Association of the Automotive Industry (VDA), the automotive industry in Germany sees itself as a pioneer of electromobility. The corresponding further development of electric drives is therefore essential for the future viability of the industry. The electric motor or wheel hub motor is a central component in the drive train of electric vehicles.
Wheel hub motor: weight reduction by using plastics technology
The new wheel hub motor is to be made more efficient and lighter by replacing existing metal components with newly developed high-performance materials made of plastics. To this end, novel UD tapes reinforced with carbon fibers are being developed. The aim is to ensure thermal stability of the matrix stiffness even up to TG ≥ 120°C. Furthermore, contact corrosion during functionalization between the materials is to be prevented.
The processes of tape deposition, surface functionalization of inserts as well as the tool-bound forming process are developed for the full-time parallel joining of several dissimilar materials. The multi-material engine component will be designed to be material and operationally stable for the elevated loading temperature and optimized for near-zero strain. A tool will be specifically developed, designed, engineered and built for the fabrication of a demonstration prototype. After production of the final demonstrator, it is validated in a test.
The "fabulous" project covers the entire value chain from innovative high-performance material development through process development, component development and quality assurance to the finished electric motor.
M.TEC: contribution and advantages
Through the fabulous project, M.TEC GmbH is expanding its existing know-how in the field of magnetic field simulation by integrating new materials and extending existing material models. In the design of multi-material components, additional new knowledge is built up, especially in the integration of the newly developed materials in thermally and mechanically highly loaded components.
It can be assumed that this newly developed knowledge is also transferable to other products in M.TEC's working environment. Possible applications lie in virtually all areas of electrical engineering, general mechanical engineering, as well as in the aviation, rail vehicle and shipbuilding industries. Use in components for fluid dynamics such as impellers, air ducts, nozzles, tumble dryers and vacuum cleaners is also conceivable. This also applies to highly stressed parts for lightweight construction. In addition, the knowledge can also serve to reduce failure probabilities in general. A corresponding transfer to the project processes at M.TEC is expected within two to three years.
Corresponding development processes are likely to change in particular through the use of the digital twin. This form of digital support will make it possible to find solutions that represent the optimum for the totality of all requirements - as opposed to the optimum based on a single requirement. This represents a great potential for minimizing the use of resources.
Project partners & responsibilities
In this research project, M.TEC is responsible for the simulative magnetic design of the motor with a multivariant optimization as well as its overall conceptual design, together with FEV. The other project partners are:
- AKRO-PLASTIC GmbH
- CirComp GmbH
- FEV Europe GmbH
- FKT Formenbau und Kunststofftechnik GmbH
- Fraunhofer IPT
- Fraunhofer LBF
- Gubesch Thermoforming GmbH
- SURAGUS GmbH
Further information on this research project
Project title: |
Funktionsintegrierte Antriebsbauteile für die Elektromobilität ermöglicht durch neuartige Hochleistungs-Verbundwerkstoffe |
Funding measure: |
The project is funded within the framework of the funding measure "From Material to Innovation" according to Art. 25 of the European Commission Regulation (EU) No. 65112014 of 17.06.2014 |
Funding reference: |
03XP0214F |
Funded by: |
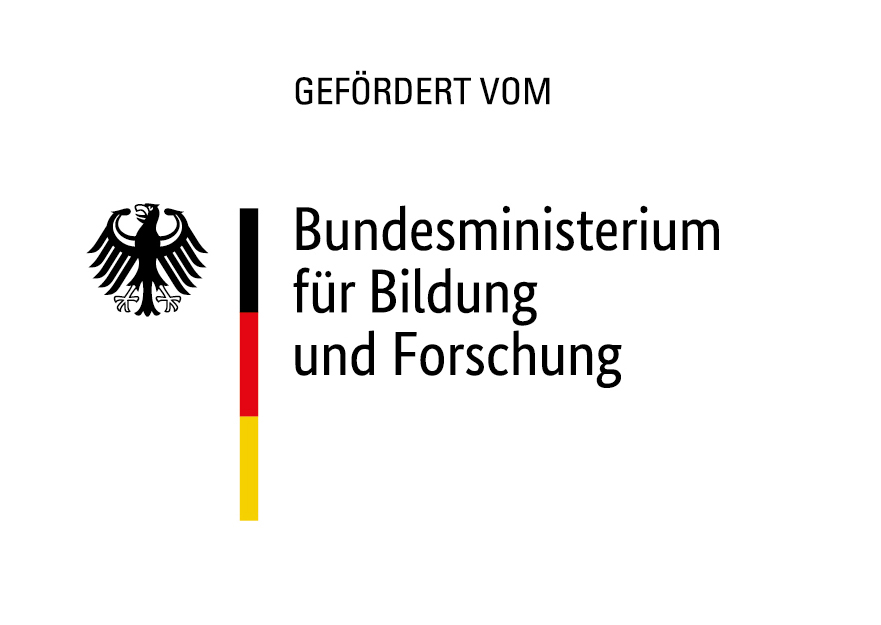 |