M.TEC develops simulation methods for multi-material lightweight materials in structural optimization
In the "LightWeightTankMat" research project, M.TEC with its simulation & calculation department is testing new, lighter plastic fuel tanks (KKB) together with three other project partners.
Lightweight synthetic tanks: Same properties, less weight
The aim of the project is a significant weight reduction with unchanged properties with regard to pollutant emission, functional integration and crash stress. Within this framework, M.TEC is developing a simulation methodology that takes into account the special properties of multi-material lightweight materials in structural optimization and thus enables the optimal component design under given boundary conditions.
Today, fuel tanks made of plastic are used in most means of transport. One technical problem is that at high operating temperatures the plastic fuel tanks have poor dimensional stability. The use of more material compensates for this, but makes them heavier and increases the CO2 consumption of the vehicle during operation. Lightweight plastic materials have the potential to solve the problem of high weight due to various positive properties. However, their development must take into account partly contradictory requirements as well as legal regulations and a cost-neutral implementation for the manufacturers.
M.TEC develops simulation methodology for structural optimization
Four project partners are involved in the research project: The company Kautex is responsible for concept development and requirements definition. Together with M.TEC, it is also working on the simulation of structures and materials. Kautex is also responsible for the production of a near-series demonstrator. The Aachen Institute of Plastics Processing (IKV) together with the Aachen Center for Integrative Lightweight Design (AZL) is involved in systematic material and process development. Together with Kautex, the AZL in turn conducts an evaluation of the material and manufacturing concept. M.TEC is responsible for simulation & calculation and CAE method development. Finally, M.TEC and Kautex work systematically on the design and dimensioning of a near-production demonstrator on this basis.
This project was funded by the European Regional Development Fund (ERDF).
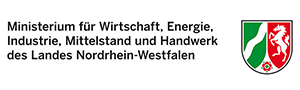